What is Demand Flow Technology: Benefits, Implementation, and Future
Unlock the power of demand flow technology. Discover its benefits, implementation, and future trends. Stand out from the competition now!
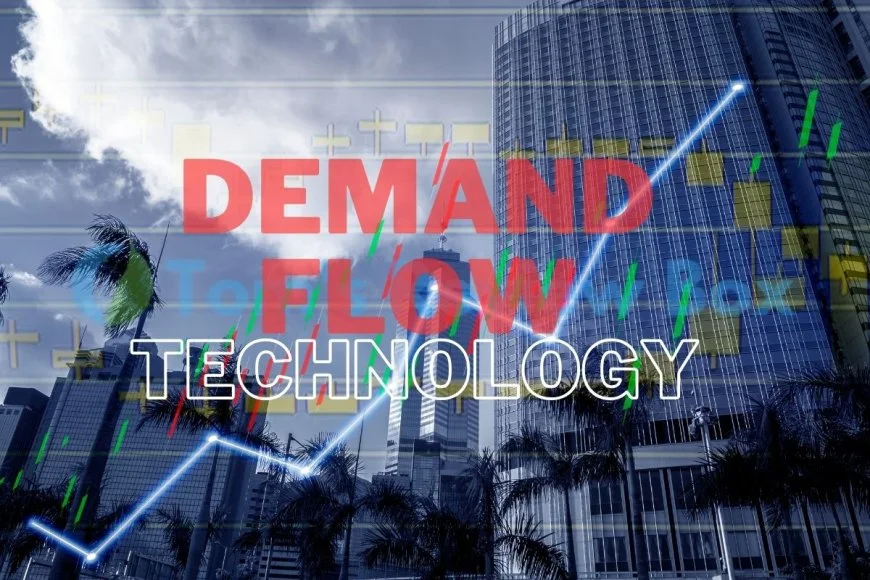
Curious about how to revolutionize your supply chain? Want to streamline production, cut down on inventories, and reduce long lead times? Enter demand flow technology. This game-changing approach focuses on responding directly to customer demand, ensuring that products are made only when needed, reducing inventories and lead time. By syncing production planning with real-time consumption patterns, it minimizes waste and maximizes efficiency. But how does it work? And what benefits can it bring to your business? In this post, we'll dive into the ins and outs of demand flow technology, exploring its principles and practical applications in today's fast-paced market.
Key Takeaways
-
Demand flow technology (DFT) optimizes production by aligning manufacturing processes with actual customer demand and capacity.
-
Implementing DFT can lead to reduced lead times, lower inventory levels, and improved production efficiency.
-
Key elements of DFT include demand forecasting, continuous improvement, synchronized production processes, and high impact.
-
DFT aligns with lean manufacturing principles, emphasizing waste reduction, material, and value stream optimization.
-
Successful case studies demonstrate how DFT can enhance supply chain management and overall operational performance.
-
Despite the benefits, adopting DFT may pose challenges related to organizational change and process integration.
Demand Flow Basics
Manufacturing Evolution
Demand Flow Technology (DFT) has revolutionized traditional manufacturing by transforming the way products are produced and delivered. The evolution of manufacturing processes has been significantly influenced by demand flow level.
Manufacturing used to be a process where products were made in large quantities based on forecasts. This often led to overproduction, excess inventory, and inefficient use of resources. However, with the introduction of demand flow technology, manufacturers shifted their focus to meeting customer demand in real-time.
This shift has allowed companies to operate more efficiently and respond quickly to changing market demands. For example, instead of producing a large batch of items that may or may not sell, manufacturers can now adjust production based on actual customer orders.
Technology Overview
Demand flow technology is a lean manufacturing strategy that is centered around meeting customer demand effectively. It utilizes real-time data to optimize production processes and minimize waste.
By integrating advanced technologies such as data analytics and automation, demand flow technology enables manufacturers to streamline their operations. For instance, predictive analytics can be used to forecast demand accurately, allowing companies to adjust their production schedules accordingly.
Moreover, DFT emphasizes the importance of continuous improvement through the use of technology-driven insights. By analyzing real-time data from various stages of production, manufacturers can identify areas for enhancement and make informed decisions about resource allocation.
Defining Demand Flow Technology
Core Principles
Demand flow technology (DFT) is rooted in the principles of efficiency, flexibility, and customer-centricity. It revolves around continuous improvement and waste reduction, making it a dynamic approach to production. At its core, DFT places significant emphasis on catering to customer demand, ensuring that production aligns with what customers want.
The principles of DFT are all about optimizing processes to meet customer needs efficiently. For instance, if a company uses DFT in their manufacturing process and realizes that there's an increasing demand for a particular product, they can quickly adjust their production schedule and inventory levels to accommodate this change. This flexibility allows companies to respond swiftly to market demands while minimizing waste through efficient resource allocation.
The focus on efficiency means that DFT aims at maximizing productivity by reducing lead times and improving overall workflow management. By integrating these core principles into their operations, businesses can create a leaner production environment that adapts seamlessly to fluctuations in demand.
DFT Components
Demand flow technology encompasses various components essential for its successful implementation. These include demand forecasting, which involves predicting future customer requirements based on historical data and market trends. Effective inventory management plays a crucial role in ensuring that sufficient stock is available without overstocking or causing unnecessary holding costs.
Moreover, components such as production scheduling help coordinate the timing of manufacturing activities with demand patterns while maintaining optimal resource utilization. Furthermore, workflow optimization ensures smooth transitions between different stages of production by identifying potential bottlenecks and streamlining processes accordingly.
When these components work together harmoniously within the framework of DFT, they contribute significantly towards creating an efficient production system capable of meeting varying levels of consumer demand without excessive stockpiling or delays.
Process Optimization
Process optimization lies at the heart of demand flow technology as it focuses on refining every aspect of production for maximum efficiency. By pinpointing inefficiencies within workflows and addressing them proactively, companies employing DFT can eliminate bottlenecks that impede productivity.
For example: If there's a specific stage in the manufacturing process where materials frequently pile up due to slow machinery or inadequate staffing levels;
Benefits of Demand Flow Technology
Increased Efficiency
Demand flow technology (DFT) aims to streamline operational efficiency in the manufacturing process. By cutting down on non-value-added activities, DFT significantly enhances overall efficiency. This means that with DFT, companies can produce more goods using the same amount of resources and time.
Implementing demand flow technology leads to a reduction in operational costs and waste. The optimized utilization of resources results in substantial cost savings for businesses. For example, by minimizing excess inventory and reducing lead times, companies can lower their production costs significantly.
Reduced Costs
One of the key outcomes of implementing demand flow technology is reduced operational costs and waste. The focus on waste reduction directly contributes to lower production costs as it eliminates unnecessary expenses associated with overproduction or excess inventory.
Cost savings are achieved through optimized resource utilization when utilizing demand flow technology. By minimizing non-value-added activities such as waiting time or excessive transportation, companies can cut down on unnecessary expenses while maintaining high productivity levels.
Enhanced Flexibility
Demand flow technology enables greater adaptability to changing customer demands and market dynamics. It emphasizes flexible production capabilities that allow manufacturers to respond swiftly to varying requirements without disrupting operations.
The hallmark of demand flow technology lies in its ability to enhance flexibility within the manufacturing process. This means that companies employing DFT can adjust their production schedules quickly based on shifting market demands without compromising quality or efficiency.
Implementing DFT in Production
Planning Stage
The planning stage of implementing Demand Flow Technology (DFT) is crucial. It involves analyzing customer demand patterns and production requirements to create a strategic framework for the adoption of DFT. By understanding these demand patterns, companies can align their production processes with actual market needs, reducing waste and increasing efficiency. Effective planning sets the foundation for successful implementation of DFT, ensuring that resources are allocated optimally to meet customer demands.
During this stage, companies strategize on how best to integrate DFT into their operations. For instance, they may assess which products are high in demand and require continuous production versus those with fluctuating demand that need a more flexible approach. This analysis helps in streamlining production processes according to the principles of DFT, focusing on creating value only when it's needed rather than building up excess inventory.
Execution Phase
The execution phase involves putting the planned strategies into action by integrating DFT into day-to-day operations. It requires aligning all aspects of production with the principles of Demand Flow Technology for seamless execution. Companies must ensure that each step in the production process adds value as per customer demand without any unnecessary delays or bottlenecks.
For example, if a company identifies through its planning stage that certain products have erratic demand patterns, they might implement a just-in-time manufacturing strategy aligned with DFT principles to avoid overproduction and excessive inventory costs.
Successful execution is pivotal because it directly impacts realizing the benefits associated with Demand Flow Technology such as reduced lead times, increased productivity levels due to streamlined processes, and improved overall operational efficiency.
Monitoring Progress
Continuous monitoring progress allows businesses to make real-time assessments of their production performance against set targets within Demand Flow Technology implementation. By tracking key metrics like cycle time reduction or inventory turnover rate, organizations can evaluate how effectively implemented strategies are performing under DFT guidelines.
This monitoring provides insights for ongoing improvements in implementing Demand Flow Technology so that adjustments can be made promptly based on real-time data analysis instead of waiting until after an entire batch has been completed or shipped out.
Key Elements of Demand Flow
Just-In-Time Production
Demand flow technology places a strong emphasis on just-in-time production to reduce inventory holding costs. This means synchronizing production with customer orders, which helps minimize excess inventory levels. The concept is deeply rooted in the lean philosophy that underpins demand flow technology. By aligning production closely with actual demand, companies can avoid overproduction and maintain a more efficient operation.
For example, let's consider a car manufacturing plant implementing demand flow technology. Instead of producing a large number of cars and storing them in warehouses, the plant would adjust its production based on current customer orders. This ensures that only the necessary amount of cars are being produced at any given time, reducing storage costs and preventing an oversupply in the market.
Customer Driven At the heart of demand flow technology lies customer-driven manufacturing. This approach prioritizes tailoring production processes to match actual customer demand patterns and preferences. Customer feedback plays a pivotal role in shaping manufacturing procedures under this methodology. By constantly analyzing consumer behavior and responding swiftly to changes in their preferences, companies can ensure that their products remain aligned with what customers truly want.
To illustrate this point further, imagine a clothing manufacturer utilizing demand flow technology. Instead of mass-producing garments based on assumptions about popular styles or colors, they would gather data from sales trends and customer feedback to guide their production decisions. This allows them to create clothing lines that directly reflect the current demands of their target audience.
Flow Manufacturing Another critical aspect of demand flow technology is flow manufacturing, which focuses on ensuring smooth material movement within the production process. By streamlining material flows through continuous improvement processes, companies can eliminate waste and enhance efficiency throughout their operations.
Demand Flow and Lean Manufacturing
Similarities
Demand flow technology (DFT) is akin to lean manufacturing in its focus on minimizing waste and continuously improving processes. Both methodologies strive to streamline operations, reduce unnecessary inventory, and enhance overall efficiency. DFT, like lean manufacturing, aims to eliminate non-value-added activities that do not contribute to the end product or service. By identifying and eliminating waste, both systems seek to optimize resources while delivering high-quality products or services.
Furthermore, both DFT and lean manufacturing emphasize the importance of employee involvement in process improvement. They recognize that frontline workers often have valuable insights into enhancing operational efficiency. By empowering employees to identify areas for improvement and participate in decision-making processes, organizations can harness their collective expertise for better outcomes.
Differences
Despite sharing similarities with lean manufacturing principles, demand flow technology distinguishes itself by placing a specific emphasis on aligning production with customer demand patterns. While lean manufacturing focuses on eliminating all types of waste throughout the production cycle, DFT goes a step further by tailoring production directly to customer needs.
Moreover, demand flow technology incorporates various components such as inventory management, workflow optimization, and real-time data analysis into its approach. This comprehensive integration allows organizations to adapt quickly to fluctuations in customer demand while maintaining efficient operations.
Synergistic Approach
Demand flow technology takes a synergistic approach by integrating multiple elements crucial for successful implementation. For instance:
-
Inventory Management: DFT emphasizes optimizing inventory levels based on actual customer demand rather than forecasts.
-
Workflow Optimization: Through careful analysis of workflows within the production process, DFT seeks to minimize bottlenecks and improve overall efficiency.
-
Real-Time Data Analysis: Leveraging real-time data enables organizations practicing DFT to make informed decisions promptly based on current market demands.
This integrated approach ensures that every aspect of the organization's operations aligns with customer requirements while minimizing wastage at every stage of production.
DFT Impact on Supply Chain Management
Inventory Reduction
One of the primary goals of demand flow technology (DFT) is to reduce excess inventory levels. By employing efficient production planning and just-in-time practices, companies can minimize the amount of stock they hold at any given time. This reduction in inventory not only helps in cutting down storage costs but also minimizes the risk of holding obsolete or expired products. For example, a company implementing demand flow technology might analyze historical sales data to forecast future demand accurately, thereby producing only what is needed when it's needed.
By reducing excess inventory, businesses can free up valuable warehouse space that can be utilized for other purposes such as expanding production lines or accommodating new product lines. This optimization leads to improved overall efficiency within the supply chain.
Supplier Relationships
Demand flow technology places a strong emphasis on fostering collaborative relationships with suppliers. By working closely with suppliers and sharing real-time information about customer demand and production schedules, companies practicing DFT aim to ensure timely delivery of materials aligned with their production needs. This close collaboration allows for better coordination between all parties involved in the supply chain process, resulting in reduced lead times and minimized disruptions due to material shortages.
Moreover, building strong supplier relationships through demand flow technology enables companies to negotiate favorable terms such as flexible pricing and shorter lead times for urgent orders. These mutually beneficial agreements contribute to creating a more agile and responsive supply chain ecosystem that can quickly adapt to changing market demands.
Logistics Optimization
Logistics optimization forms an integral part of demand flow technology, focusing on efficient material handling and distribution processes within the supply chain network. Companies implementing DFT evaluate their transportation routes, warehouse layouts, and packaging methods to identify opportunities for streamlining operations while minimizing costs associated with transportation and warehousing.
For instance, by strategically locating distribution centers closer to major markets or customers' locations, businesses can significantly reduce transit times and shipping expenses while ensuring faster order fulfillment. Furthermore, leveraging advanced technologies like RFID (Radio-Frequency Identification) systems or automated picking solutions enhances visibility into inventory movement across different stages of the logistics process—enabling better tracking capabilities and proactive management of potential bottlenecks.
Case Studies of DFT Success
Industry Examples
Several industries, such as automotive and electronics, have embraced demand flow technology (DFT) to streamline their manufacturing processes. In the automotive sector, companies have utilized DFT to optimize production efficiency by aligning production with consumer demand. For instance, a car manufacturer employing DFT can adjust its production based on real-time market demands for specific vehicle models or features. This flexibility allows them to reduce excess inventory and respond promptly to changes in customer preferences.
Similarly, in the electronics industry, DFT has been instrumental in managing inventory levels more effectively. By using this approach, electronic manufacturers can minimize overproduction and better match supply with fluctuating consumer demand for various electronic devices like smartphones or laptops. As a result, they can avoid stockpiling outdated products while swiftly adapting to new trends and technological advancements.
Performance Metrics
Under demand flow technology, organizations closely monitor key performance indicators (KPIs) such as cycle time reduction and on-time delivery rates. Cycle time refers to the total time taken to produce an item from start to finish. With DFT implementation, companies strive to shorten this duration by eliminating non-value-added steps in their production processes. By doing so, they enhance operational efficiency and responsiveness while minimizing lead times.
Moreover, maintaining high on-time delivery rates is critical when applying demand flow technology. It ensures that products are delivered according to customers' expectations without delays or disruptions due to inadequate inventory management or inefficient manufacturing practices. Consequently, businesses utilizing DFT aim for exceptional reliability in meeting customer demands promptly and consistently.
Lessons Learned
Implementing demand flow technology necessitates organizations learning from past experiences and continuously refining their processes based on insights gained through data analysis and feedback mechanisms. Companies must remain adaptable and open-minded during this journey of improvement as they encounter challenges unique to their operations.
For example:
-
A company may realize that certain product lines require different demand forecasting approaches than others.
-
They might discover bottlenecks within specific stages of the production process that need addressing.
-
Organizations could also learn how external factors like seasonal fluctuations impact demand patterns for their products.
Challenges in Adopting DFT
Organizational Resistance
Resistance within organizations may arise during the implementation of demand flow technology due to changes in established workflows and practices. When a company introduces DFT, employees might resist the new approach because they are comfortable with traditional methods. For example, workers who have been accustomed to batch production might find it challenging to switch to a more flexible and demand-driven model. This resistance can stem from fear of change or uncertainty about how their roles will evolve within the new system.
Moreover, implementing DFT requires significant changes in processes and mindsets, which can be met with skepticism by those comfortable with existing procedures. To overcome this challenge, companies need effective change management strategies that involve clear communication about the benefits of DFT and how it aligns with organizational goals. By involving employees in the transition process through training and open dialogue, organizations can mitigate resistance and create a more supportive environment for adopting demand flow technology.
Training Requirements
Training programs are essential for equipping employees with the necessary skills and knowledge to effectively operate within a demand flow technology environment. Employees must understand how DFT differs from traditional manufacturing methods so that they can adapt their work habits accordingly. For instance, workers need training on lean principles, pull-based systems, inventory management techniques specific to DFT, and problem-solving methodologies such as Six Sigma.
Furthermore, cross-functional training is crucial as various departments must collaborate seamlessly under a demand-driven approach. This means providing opportunities for employees across different functions to learn about each other's roles within the context of demand flow technology. Investing in comprehensive training not only ensures smooth adoption but also empowers employees to contribute actively towards improving operational efficiency through continuous learning.
Continuous Improvement
Continuous improvement is ingrained in the culture fostered by demand flow technology, driving ongoing enhancements across all aspects of manufacturing operations. With DFT, companies continually seek ways to eliminate waste, improve quality control measures, optimize production schedules based on actual customer demands rather than forecasts alone—among other improvements aimed at enhancing overall efficiency.
Implementing continuous improvement initiatives often involves changing entrenched processes or mindsets that resist change; therefore fostering an environment where innovation is encouraged becomes vital for success under demand flow technology.
Future of Demand Flow Technology
Technological Advancements
Advancements in digital technologies have significantly improved demand flow technology. With the integration of advanced software and real-time data analysis, companies can now gain deeper insights into their production processes. This allows for better decision-making and more efficient resource allocation. For example, by analyzing real-time demand patterns, manufacturers can adjust their production schedules to meet fluctuating customer needs, reducing waste and optimizing resources.
Moreover, automation plays a crucial role in enhancing demand flow technology. Automated systems can streamline the entire manufacturing process by autonomously adjusting production levels based on market demands. This not only improves operational efficiency but also minimizes human errors, leading to higher product quality.
In addition to this, predictive maintenance is another technological advancement that has revolutionized demand flow technology. By leveraging sophisticated algorithms and sensor data from equipment, companies can predict potential machine failures before they occur. This proactive approach reduces downtime and maintenance costs while ensuring continuous operations.
Industry 4.0 Integration
The integration of demand flow technology with Industry 4.0 concepts opens up new possibilities for interconnected manufacturing systems and smart factories. Through seamless connectivity between machines, products, and humans (IIoT), companies can achieve unprecedented levels of flexibility and customization in their production processes.
For instance, by utilizing cyber-physical systems within smart factories, manufacturers can create self-regulating production lines that adapt to changing demands in real time without human intervention. This level of agility enables businesses to respond swiftly to market trends while maintaining high productivity levels.
Furthermore, the incorporation of artificial intelligence (AI) into demand flow technology enhances predictive analytics capabilities even further. AI algorithms can analyze vast amounts of historical data to forecast future demand patterns accurately—empowering organizations with valuable foresight for planning inventory levels and optimizing supply chain management.
Sustainable Manufacturing
Demand flow technology aligns with sustainable manufacturing practices by promoting resource optimization and waste reduction across the production cycle. By minimizing overproduction through accurate demand forecasting, manufacturers reduce unnecessary inventory buildup—leading to lower energy consumption and reduced material wastage. Additionally, the streamlined operations facilitated by demand flow technology contribute towards overall environmental sustainability by decreasing carbon emissions associated with excessive transportation or idle machinery use.
Summary
Congratulations! You've now gained a comprehensive understanding of demand flow technology (DFT). From its basics and key elements to its impact on production, supply chain management, and lean manufacturing, you've explored the ins and outs of DFT. The case studies provided real-world examples of DFT's success, while also shedding light on the challenges in adopting this innovative approach. Looking ahead, the future of demand flow technology promises exciting developments that could reshape production and supply chain strategies.
Now equipped with this knowledge, consider how demand flow technology could revolutionize your own industry or business. Embracing DFT's principles and practices could lead to enhanced efficiency, reduced waste, and improved responsiveness to market demands. Take the next step by evaluating how DFT can be integrated into your operations, and explore the potential benefits it holds for your organization.
Frequently Asked Questions
What are the key elements of Demand Flow Technology?
Demand Flow Technology (DFT) relies on crucial elements such as demand-driven production, continuous flow manufacturing, and synchronized supply chain management to optimize processes and minimize waste.
How does Demand Flow Technology impact supply chain management?
By synchronizing production with customer demand, DFT reduces inventory levels, shortens lead times, improves order fulfillment rates, and enhances overall visibility and responsiveness within the supply chain.
What are the benefits of implementing Demand Flow Technology in production?
Implementing DFT can result in improved productivity, reduced lead times, lower operating costs, enhanced product quality, increased flexibility to meet changing demands, and ultimately higher customer satisfaction.
What challenges might a company face when adopting Demand Flow Technology?
Challenges in adopting DFT may include resistance to change from employees or management, the need for significant process reengineering, initial investment costs for technology and training programs, as well as potential disruptions during implementation.
How does Demand Flow relate to Lean Manufacturing principles?
Demand Flow complements Lean Manufacturing by focusing on eliminating waste through continuous flow manufacturing based on actual customer demand rather than forecasts. Both share the goal of optimizing efficiency while maintaining high-quality standards.
What's Your Reaction?
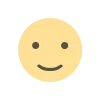
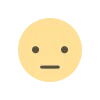
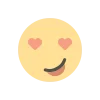
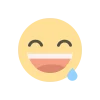
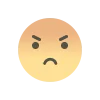
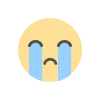
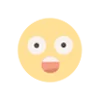